So, how can manufacturers overcome these pain points? What is the solution to efficient work order management? The answer lies in implementing a robust work order management system that leverages technology and automation to streamline processes, improve visibility, and enhance collaboration. By adopting digital solutions specifically designed for work order management, manufacturers can optimize resource allocation, eliminate manual errors, improve communication, and achieve operational excellence.
The Power of Effective Work Order Management
Work order management is a critical component of organizational success, enabling businesses to streamline projects and processes for optimal efficiency and improved outcomes. By implementing effective work order management strategies, companies can achieve higher productivity levels, enhance collaboration among teams, and drive overall business growth.
Here are key aspects of work order management
- Streamlined Workflows
- Improved Collaboration
- Enhanced Visibility
- Task Prioritization
- Resource Optimization
- Continuous Improvement
- Real-Time Monitoring and Reporting
Effective work order management is a key driver of organizational productivity and success. By streamlining workflows, improving collaboration, and optimizing resources, businesses can achieve higher efficiency, better outcomes, and a competitive edge in the market.
Differentiating Work Order Management from Project Management
It is crucial to understand the distinction between work order management and project management, as they serve different purposes within an organization. While project management focuses on planning and executing specific projects, work order management has a broader scope, encompassing the planning, management, and optimization of critical business processes.
Work Order Management
Work order management involves the planning, coordination, and optimization of various tasks and processes across the organization. Its primary objective is to improve work planning processes, streamline resource allocation, and drive long-term results. By effectively managing work orders, organizations can enhance productivity, boost employee motivation, and achieve overall operational excellence.
Project Management with Complex Jobs Structure
Project management, on the other hand, is centered around the successful execution of individual projects. It includes defining project goals, creating project plans, allocating resources, monitoring progress, and ensuring project completion within specific timelines and budget constraints. The primary focus of project management is to deliver project-level success by meeting objectives, delivering desired outcomes, and satisfying client requirements.
While work order management looks beyond the boundaries of individual projects and focuses on continuous improvement and resource optimization across the organization, project management concentrates on achieving specific project goals within defined timeframes and budgets.
Work order management and project management are distinct yet interconnected aspects of organizational management. By understanding their differences and leveraging their respective strengths, businesses can effectively manage both ongoing processes and individual projects, leading to enhanced efficiency, productivity, and overall success.
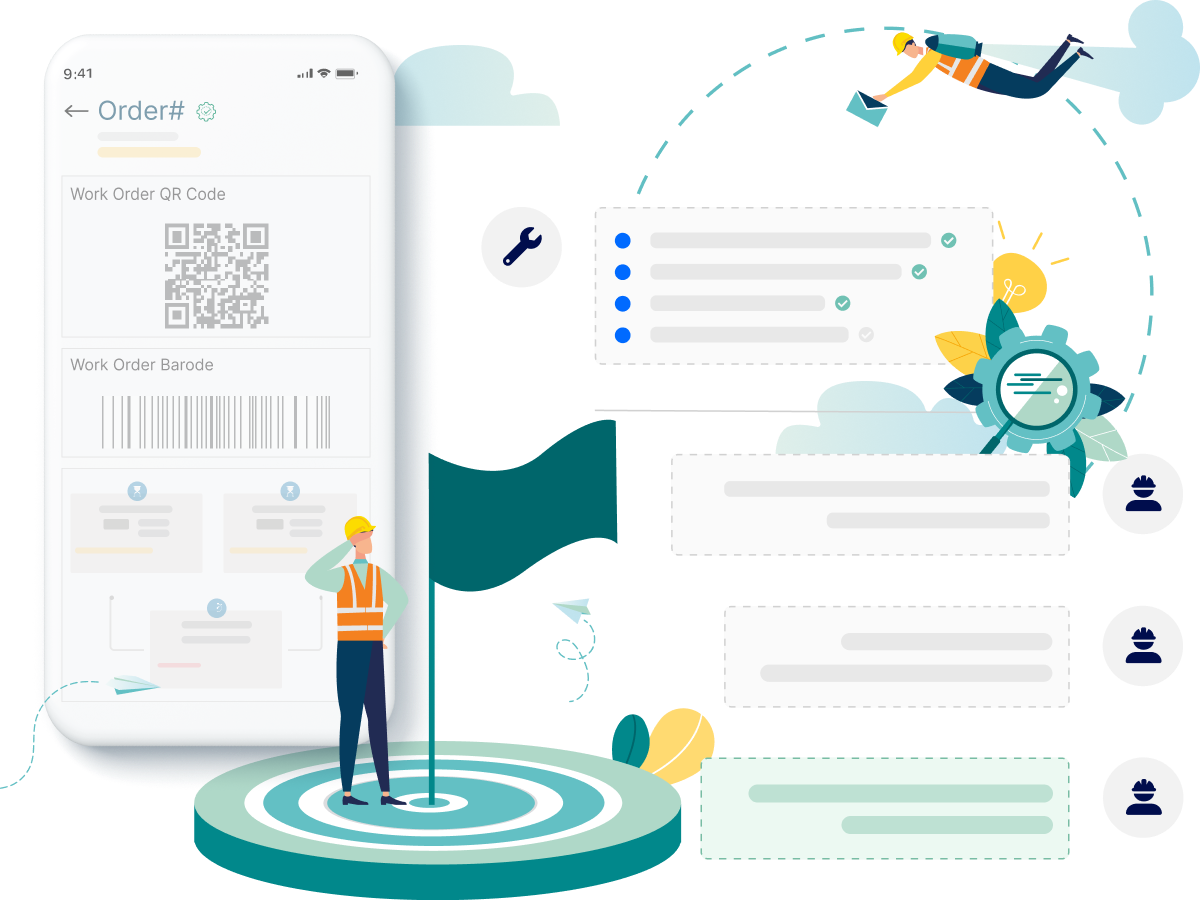
Maximizing Throughput: The Game-Changing Significance of Effective Jobs Scheduling in Manufacturing.
The Significance of Effective Jobs Scheduling on Factory Throughput
Work order management plays a vital role in streamlining and optimizing processes, projects, and routine tasks within an organization. By establishing a comprehensive organizational workflow, work order management ensures that teams have the necessary context and information to perform their work effectively. It provides stakeholders with an overview of ongoing, in-progress, and completed projects while highlighting how each piece of work contributes to overall business objectives and success.
Feeding Team Context and Information
By centralizing information and updates, work order management ensures that teams have access to the necessary context for their work. This facilitates better decision-making, enhances collaboration, and promotes a shared understanding of project goals and progress.
Overview of Projects
Work order management platforms provide stakeholders with a clear overview of ongoing, in-pipeline, and completed projects. This visibility allows for effective project tracking, resource allocation, and prioritization.
Contribution to Business Objectives
Work order management emphasizes the connection between individual tasks and the broader organizational objectives. It highlights how each piece of work contributes to the success of the business, fostering a sense of purpose and alignment among employees.
The benefits of effective work order management are manifold
Reduced Silos
By promoting collaboration and information sharing, work order management breaks down silos between teams and departments. This facilitates cross-functional cooperation, knowledge exchange, and more efficient workflows.
Efficient Processes
Work order management helps optimize processes by eliminating redundancies and streamlining workflows. By providing clear guidelines and standardized procedures, it minimizes errors and delays, resulting in increased operational efficiency.
Resource Optimization
With access to comprehensive information, managers can assign work that matches employees' strengths and interests. This reduces boredom, improves job satisfaction, and optimizes resource utilization, preventing both overutilization and underutilization.
Increased Motivation
Effective work order management provides employees with the necessary tools, information, and structure to perform their best work. This enhances motivation and engagement, leading to higher productivity and job satisfaction.
Work order management is essential for organizations seeking to maximize productivity, foster collaboration, and achieve their business objectives. By providing context, visibility, and alignment, work order management enables teams to work efficiently, optimize resources, and drive overall success.
Exploring the Traits of Good work order management
Good work order management is characterized by a focus on work efficiency, which can be measured through indicators such as employee engagement, resource utilization, and business outcomes. A robust work order management system centralizes data, documents processes, aligns with business goals, and fosters team collaboration.
Here are the key elements of a good work order management system
Employee Engagement and Motivation
A good work order management system promotes employee engagement and motivation by providing clear goals, meaningful work, and opportunities for professional growth. It empowers employees to take ownership of their tasks and encourages their active participation in decision-making processes.
Efficient Resource Utilization
Effective work order management ensures that resources, including time, skills, and tools, are allocated efficiently. It minimizes waste, avoids overburdening employees, and optimizes resource utilization to achieve optimal productivity and cost-effectiveness.
Better Business Outcomes
Good work order management contributes to better business outcomes by aligning work processes with overall organizational goals and objectives. It enables teams to focus on tasks that have the most significant impact on achieving desired outcomes, leading to improved productivity, customer satisfaction, and profitability.
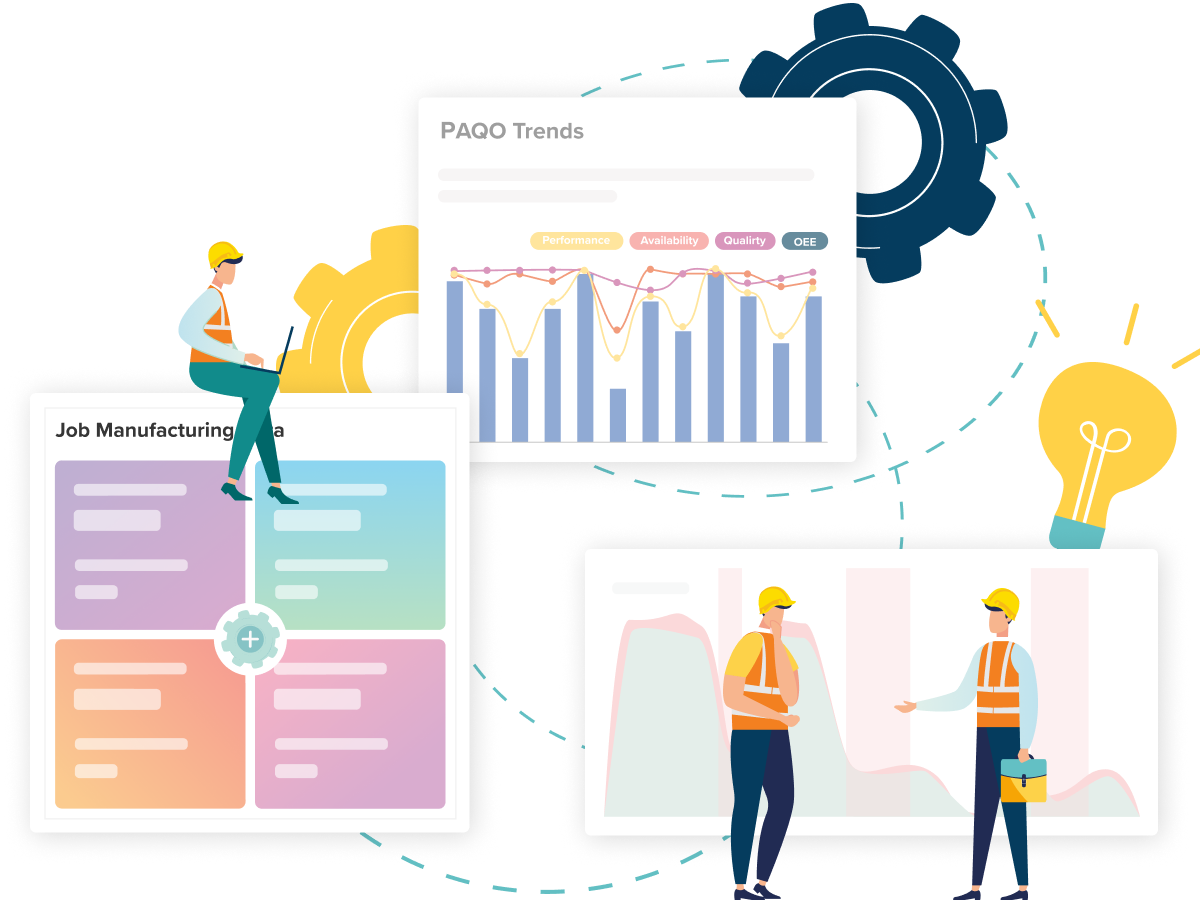
Mastering Efficiency: The Essential Components for Crafting an Agile Work Order Management System.
Creating an efficient work order management system involves the following steps:
Implementing a robust Work order management system requires careful planning and consideration.
Here are the 4 key points
Comprehensive Planning
Thorough planning is crucial to define work processes, establish realistic timelines, and allocate resources effectively. It involves assessing project requirements, setting clear goals, and identifying potential challenges or bottlenecks.
Employee Engagement
Engage with employees to understand their pain points, challenges, and suggestions for improvement. Actively involve them in the decision-making process, allowing them to provide input and insights based on their experiences and expertise.
WorkOrder Management Software
Implementing work order management software can streamline and automate various aspects of work order management, including task allocation, progress tracking, and reporting. Choose a software solution that aligns with your organization's needs and promotes collaboration among team members.
Collaboration and Content Management Tools
Integrate collaboration and content management tools into your work order management system to facilitate seamless communication, document sharing, and knowledge exchange. This helps teams collaborate effectively, access relevant information, and stay organized.
By incorporating these elements and practices into your work order management approach, you can create an efficient system that drives productivity, empowers employees, and contributes to the overall success of your organization.
The Step-by-Step Guide to Implementing Effective Jobs Management on the Shopfloor
Implementing a robust Work order management system requires careful planning and consideration. By following a step-by-step approach, organizations can create a framework that optimizes resource utilization, improves employee retention, and enhances customer satisfaction. Keep in mind that the specific steps may vary depending on factors such as organization size, team culture, and existing process efficiency. Here is a foundational guide to help you get started:
5 Steps to Implement Smart Jobs Scheduling
Step 1: Set Work order management Goals and Objectives:
- Take inventory of current and past projects, processes, and existing challenges.
- Conduct surveys and one-on-one discussions to identify the barriers faced by teams.
- Define clear, measurable goals based on the identified problems and desired improvements.
- Examples of goals include creating new processes, streamlining current processes, and enhancing cross-functional collaboration.
Step 2: Create a Workflow Blueprint with an Implementation Schedule:
- Develop tactical plans to achieve each goal identified in the previous step.
- Seek feedback from key team members to ensure comprehensive coverage and address blind spots.
- Outline a clear implementation schedule for executing the identified tactics.
Step 3: Select Tools to Support the Work order management Plan:
- Identify software tools that align with the tactics outlined in the workflow blueprint.
- Consider content management tools for documentation, collaboration, and knowledge management.
- Choose communication software to facilitate team and cross-functional collaboration.
- Explore Work order management software that enables project planning, resource management, reporting, and forecasting.
Step 4: Implement the Work order management System:
- Execute the planned implementation based on the existing systems and processes.
- Document business goals, objectives, processes, and ongoing projects.
- Establish a centralized data repository for easy access to relevant information.
- Create a resource inventory with a skills gap analysis and employee strengths and interests.
- Provide training resources on the new tools and processes introduced.
- Communicate the changes to team leads and ensure they explain the new processes to their respective teams.
Step 5: Measure Results and Iterate as Needed:
- Track the progress and effectiveness of the implemented Work order management system.
- Share the results with employees to demonstrate the impact of their efforts.
- Gather feedback from employees to assess how well the new processes have addressed their concerns.
- Use the results and feedback to identify areas for further optimization and continuous improvement.
By following these steps, organizations can establish an efficient Work order management system that promotes productivity, collaboration, and customer satisfaction. Regular evaluation and adaptation ensure ongoing success and the ability to address evolving needs.
Real-time Production Data Points.
Take the next step to digitalize your site!
Shopfloor Monitoring Dashboard for Industry 4.0
Production Workflow Management for Shopfloor
The Role of Work order management Software in Driving Organizational Efficiency
Work order management software plays a crucial role in streamlining and optimizing organizational processes, enhancing productivity, and driving business results. It enables organizations to understand where their time is spent and how it can be better utilized.The software facilitates efficient planning, management, and tracking of routine tasks within projects. With its ability to assign tasks based on priority of the work, Work order management software ensures optimal resource allocation.
It empowers organizations to take on projects based on resource availability and team capacity, driving better resource management and capacity planning.
These capabilities contribute to improved business outcomes, increased team performance, and enhanced employee well-being.
When selecting Work order management software, it is essential to choose a solution that enables comprehensive management of tasks, projects, and resources in one centralized platform.
The software should provide different project views, such as Gantt charts and bar charts, to facilitate effective project planning and tracking.
Reporting capabilities are also crucial for keeping both employees and stakeholders up-to-date on project progress. Additionally, seamless integration with team collaboration and content management tools further streamlines processes and enhances overall efficiency.
By leveraging the benefits of Work order management software, organizations can drive organizational efficiency, achieve better results, and foster a positive work environment.
Strategies for Improving Work order management Efficiency
Improving Work order management efficiency is a continuous process that involves adopting effective strategies and implementing practical solutions. By enhancing Work order management practices, organizations can optimize processes, maximize productivity, and achieve better outcomes. Here are some detailed strategies to improve your Work order management efficiency:
Top ways to Implement a Continuous Improvement Plan for the Production Planning
1. Skills and Interest Assessment
Regularly assess employees' skills, strengths, and interests to gain insights into their capabilities and preferences. Conduct performance reviews, engage in open conversations, and provide opportunities for professional development. This information helps in aligning tasks with employees' skill sets, enabling them to contribute their best work and enhancing overall team performance.
2. Streamline Processes
Thoroughly review existing processes to identify inefficiencies, bottlenecks, and unnecessary steps. Eliminate redundant tasks and automate manual processes using workflow automation tools. This streamlining eliminates time-consuming and non-value-added activities, improving overall efficiency and enabling employees to focus on high-priority tasks.
3. Establish an Information Repository
Create a centralized and easily accessible repository, such as an internal wiki or knowledge management system. This repository should house essential information such as business goals, ongoing projects, standard operating procedures, and best practices. Regularly update and organize the repository to ensure employees can quickly find and reference the information they need. This streamlines decision-making, reduces errors, and enhances collaboration across teams.
4. Reduce Meetings and Optimize Communication
Evaluate the necessity of meetings and consider alternative communication methods. Implement guidelines to determine when a meeting is truly necessary and ensure that attendees have a clear agenda and purpose. Encourage the use of asynchronous communication tools, such as chat platforms or project management software, for quick updates and discussions. By reducing unnecessary meetings and optimizing communication, you can save time, minimize interruptions, and improve productivity.
5. Learn from Others and Seek Continuous Improvement
Engage in ongoing learning and benchmarking to stay informed about industry trends and best practices. Read books, attend conferences, participate in webinars, and engage with professional networks to gain insights from experts and peers. Actively seek feedback from employees and stakeholders, encouraging suggestions for process improvements and innovations. Embrace a culture of continuous improvement, fostering a mindset of adaptability and growth.
6. Change Management and Employee Engagement
When implementing changes, involve employees from the beginning to foster buy-in and engagement. Clearly communicate the reasons behind the changes, the expected benefits, and the support available throughout the transition. Encourage open dialogue, listen to employees' concerns, and address them proactively. By involving employees in the decision-making process, you can increase their ownership and commitment to the new Work order management practices.
7. Leverage Technology
Explore Work order management software and tools that align with your organization's needs. Look for platforms that offer comprehensive features such as task management, project planning, resource allocation, and reporting. Choose tools that integrate well with other systems and collaborate seamlessly with team communication and collaboration platforms. Leveraging technology streamlines processes, improves transparency, and enhances overall Work order management efficiency. Check how If Else Cloud's modern cloud architecture supports these functionality.
By implementing these strategies and continuously refining your Work order management practices, you can create a culture of efficiency, collaboration, and continuous improvement. This will lead to improved productivity, employee satisfaction, and the achievement of organizational goals.
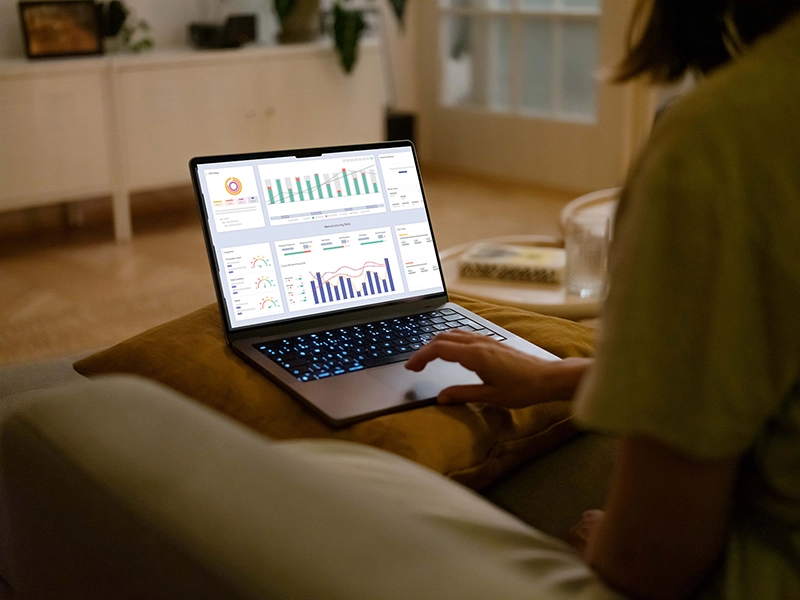
Unlock Efficiency: IfElseCloud's Cutting-Edge Solution Streamlining Work Order Management at Your Fingertips.
Transform Your Work order management with IfElseCloud: Building an Efficient System
IfElseCloud is the ideal solution for organizations seeking to create an efficient Work order management system. With its user-friendly interface and powerful features, IfElseCloud empowers teams to optimize processes and enhance productivity.
By leveraging IfElseCloud's comprehensive suite of tools, including task management, resource allocation, and reporting, organizations can streamline workflows and improve collaboration.
With the ability to customize the software to fit specific needs, IfElseCloud ensures a seamless integration into existing Work order management practices.
Moreover, IfElseCloud provides training and ongoing support to help teams fully utilize the platform's capabilities, enabling them to maximize efficiency and achieve their goals.

Empower Your Operations: Discover Why Streamlined Work Order Management is Essential, and Take Action with IfElseCloud for Unparalleled Efficiency.
Why should you care? And what to do if you do.
Implementing an efficient work order management system is crucial for manufacturers seeking to optimize their operations and drive success. By addressing the pain points associated with manual processes, resource allocation challenges, and communication gaps, manufacturers can significantly improve productivity, reduce costs, and enhance customer satisfaction.
Our product offers a comprehensive solution to streamline work order management and overcome these challenges. Let's take a closer look at some of the key features:
Production Board
Our product provides a user-friendly production board that offers a visual representation of work orders, allowing for easy tracking and monitoring of progress. This feature ensures real-time visibility into production status and helps teams prioritize tasks effectively. Read more here.
Work Order Management
With our work order management feature, you can efficiently create, assign, and track work orders. This eliminates the need for manual processes and paper-based systems, streamlining workflows and reducing errors. See how Workder Order Management works.
Maintenance Planner
Our product includes a maintenance planner that enables proactive maintenance scheduling and resource allocation. This feature helps prevent breakdowns, optimize equipment performance, and minimize production downtime. See how Maintenance Planner works.
Shopfloor Intelligence
Our shopfloor intelligence feature provides real-time insights and analytics to monitor shopfloor performance and identify areas for improvement. This data-driven approach empowers manufacturers to make informed decisions and optimize operations. See how Digital Shopfloor Intelligence works.
Reporting and Insights
Our product offers comprehensive reporting capabilities, allowing you to generate customized reports and gain valuable insights into work order status, resource utilization, and overall operational performance.
Additionally, our product leverages advanced technologies such as machine learning and AI to provide real-time insights and predictions, enabling proactive decision-making and continuous improvement. It seamlessly integrates with various systems, including IIoT, SCADA, OPCUA, ERP, and other on-prem systems, ensuring data synchronization and a holistic view of manufacturing operations. See how Reporting and Insights works.
By harnessing these powerful features, our product revolutionizes work order management, driving efficiency, productivity, and operational excellence in the manufacturing industry. Take the next step towards optimizing your work order processes and unlock the full potential of your manufacturing operations with our innovative solution.